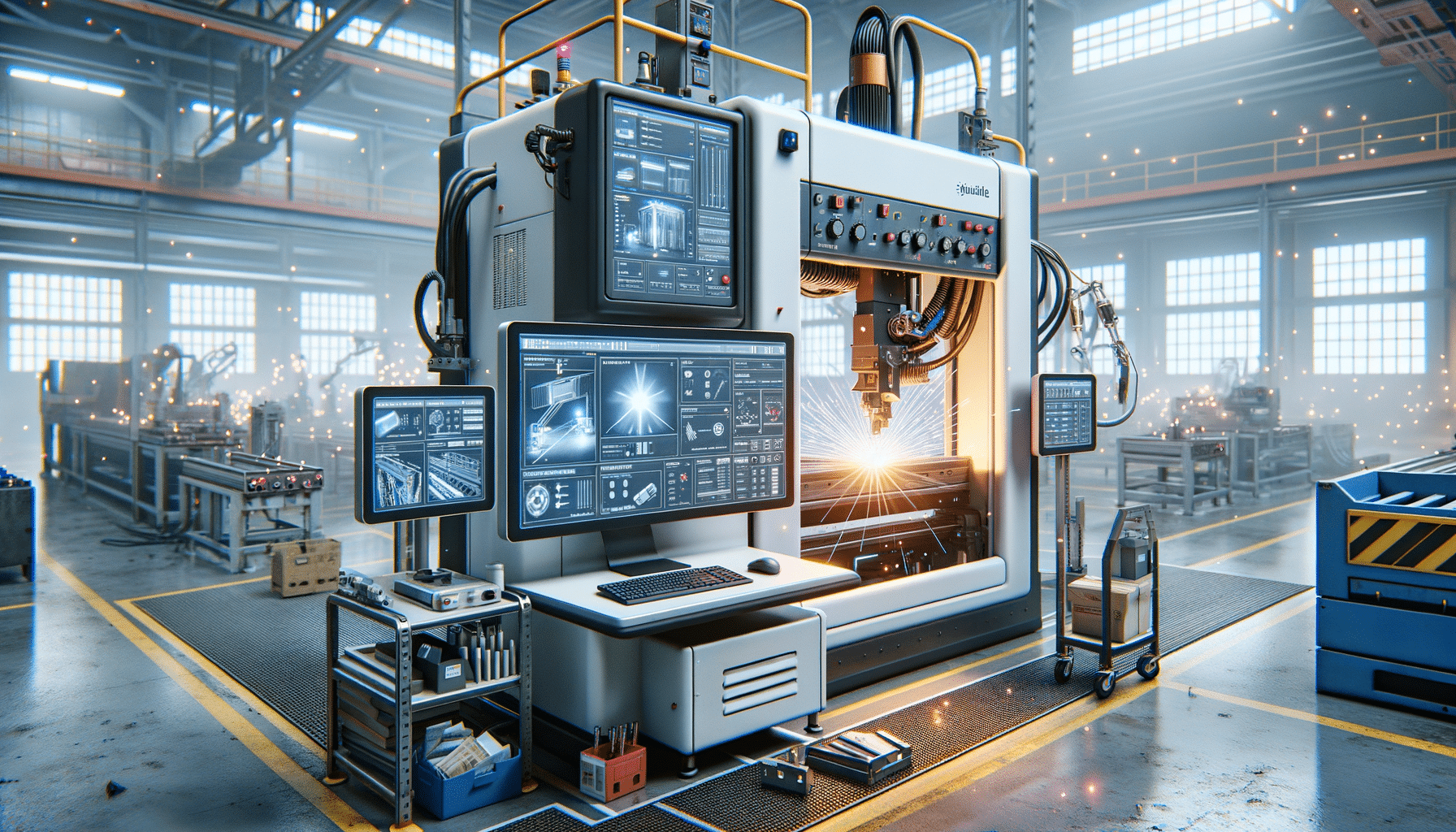
Maximize Your Welding Operations with Automation – The Key Benefits of Automated Welders
Introduction to Automated Welding Machines
In the modern landscape of manufacturing and metalworking, welding machines have always played a pivotal role. However, with advancements in technology, traditional manual welding is being complemented and, in some cases, replaced by automated welding systems. These machines are designed to increase efficiency, precision, and safety in welding operations. Automated welders are particularly beneficial in industries where large-scale production and consistent quality are paramount. Understanding the impact of automation in welding can provide insights into its potential benefits and applications.
The Advantages of Automation in Welding
Automated welding machines offer numerous advantages that make them a valuable asset in industrial settings. One of the primary benefits is the significant increase in productivity. Automated systems can operate continuously without the need for breaks, unlike human welders who require rest and are subject to fatigue. This continuous operation allows for higher throughput and faster completion of projects.
Another key advantage is the consistency and precision that automated welders provide. Unlike manual welding, where human error can lead to inconsistencies, automated systems ensure uniformity in every weld. This precision is crucial in industries where the quality of welds directly impacts the safety and functionality of the final product.
Additionally, automated welding enhances safety by reducing the need for human operators to be in close proximity to hazardous welding environments. By minimizing human involvement, the risk of accidents and exposure to harmful fumes and intense heat is significantly reduced.
Applications of Automated Welding Machines
Automated welding machines are widely used across various industries, each benefiting differently from the technology. In the automotive industry, for example, automated welders are essential for the mass production of vehicle components, ensuring each part meets strict quality standards. The aerospace industry also relies on automated welding for the construction of aircraft parts, where precision is critical to ensure safety and performance.
In the construction sector, automated welding machines are used for fabricating structural components, providing the strength and durability required for modern architecture. The oil and gas industry also employs automated welders to construct pipelines and other infrastructure, where the reliability of welds is crucial to prevent leaks and ensure safety.
These diverse applications highlight the versatility of automated welding machines and their ability to meet the demands of various sectors.
Challenges in Implementing Automated Welding Systems
Despite the numerous benefits, implementing automated welding systems comes with its own set of challenges. One of the primary obstacles is the initial cost of investment. Automated welding machines and the necessary infrastructure can be expensive, which may be a barrier for small to medium-sized enterprises.
Moreover, the integration of automated systems requires skilled personnel to operate and maintain the machinery. This need for specialized training can pose a challenge, especially in regions where there is a shortage of skilled workers.
Another challenge is the adaptation of existing processes to accommodate automation. Companies may need to redesign workflows and production lines, which can be time-consuming and costly. However, with careful planning and investment in training, these challenges can be overcome, allowing businesses to reap the benefits of automation.
Future Trends in Welding Automation
The future of welding automation looks promising, with advancements in technology poised to further enhance the capabilities of automated welding machines. One emerging trend is the integration of artificial intelligence (AI) and machine learning, which can optimize welding processes by analyzing data and making real-time adjustments to improve efficiency and quality.
Another trend is the development of collaborative robots, or cobots, which are designed to work alongside human operators. These robots can assist in welding tasks, providing flexibility and adaptability in production environments.
Additionally, advancements in sensor technology and real-time monitoring systems are expected to improve the precision and reliability of automated welding. These innovations will allow for better quality control and reduced downtime, further increasing the appeal of automation in welding.
As these trends continue to evolve, businesses that embrace automation will likely gain a competitive edge in the market.